Ready-mix concrete: A solid foundation for building the future
Elevate construction to new heights of quality with ready-mix concrete
Build with ready-mix concrete for a strong and sustainable structure
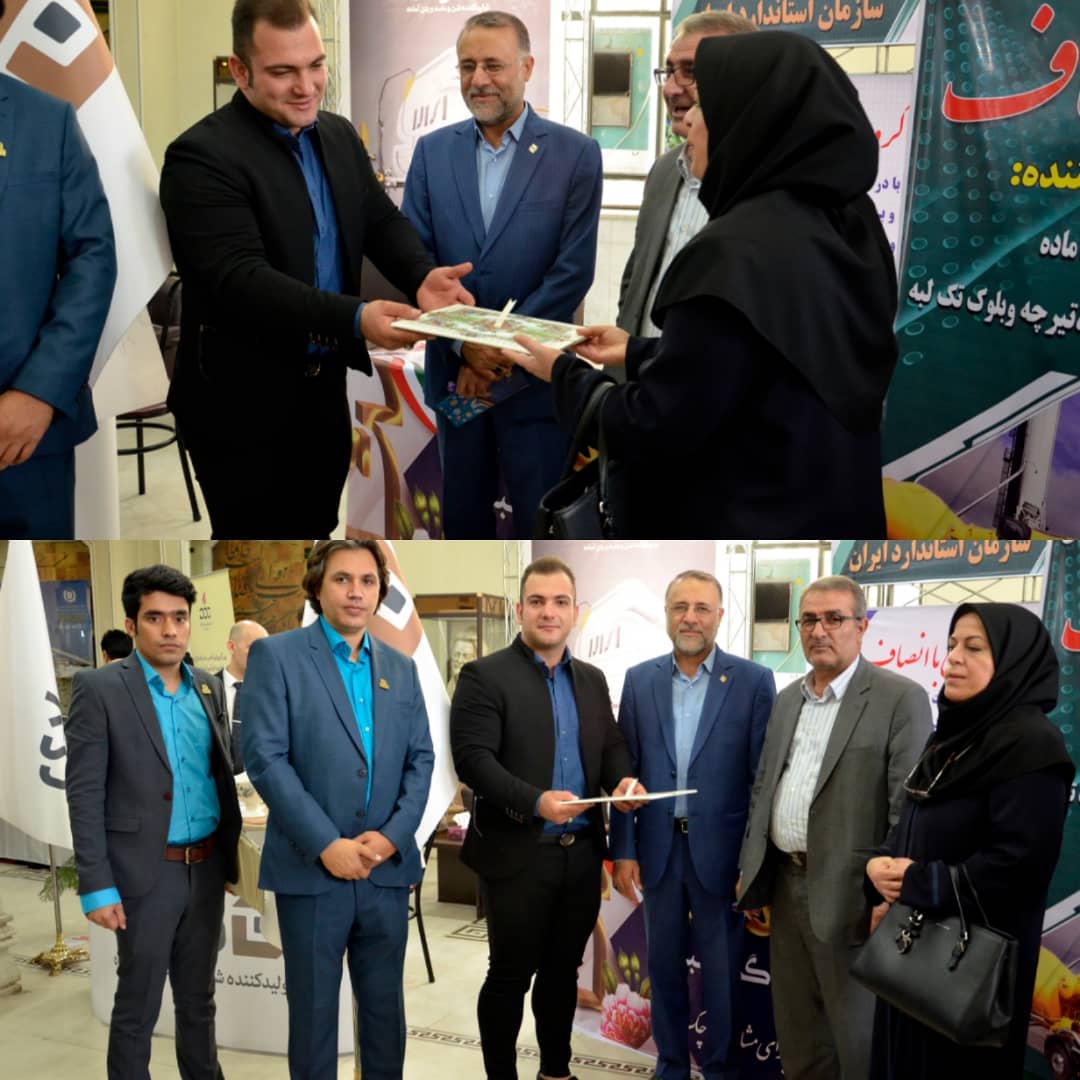
Our licenses: Trust and reliability serving you with high standards.
We provide high-quality and secure services with valid licenses and certifications. By adhering to ethical principles and professional standards, we are the best choice for you. Trusting our licenses brings you peace of mind and confidence.
Fair-Mix Ready-Mix Concrete, strengthens modern construction!
"We strive to provide services with high standards, ensure efficient resources, and offer suitable solutions to meet customer needs, aiming to be recognized as a trusted name in the ready-mix concrete industry."
Fair-Mix Ready-Mix Concrete Company is a manufacturer of high-quality and reliable ready-mix concrete. By utilizing advanced equipment and implementing rigorous quality control measures, we produce concrete that meets international standards and possesses desirable characteristics. Our primary goal is to provide ready-mix concrete services with trust and customer satisfaction.
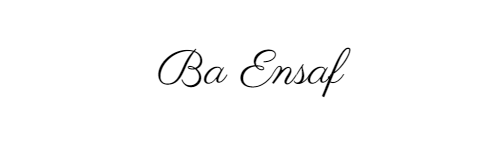
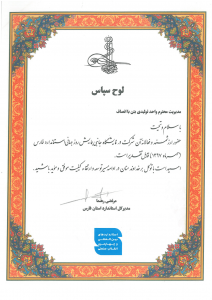
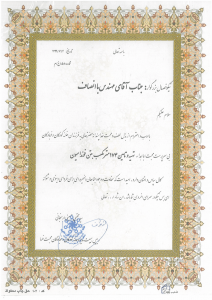
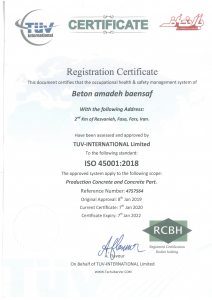
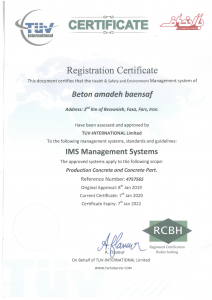
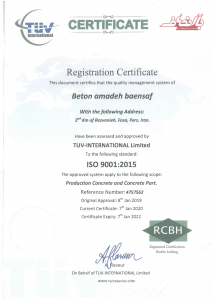
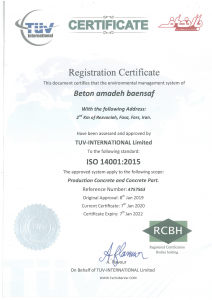
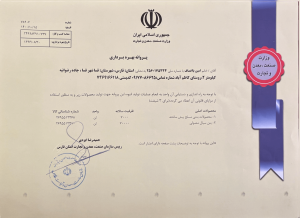
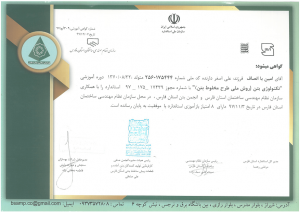
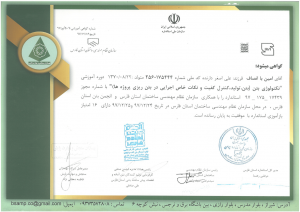
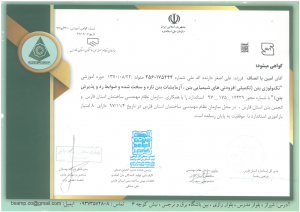
Our services
Experience the best services from our company.
Moist Ready-Mix Concrete, also known as uncured concrete, refers to a type of concrete that remains moist when transferred to other parts of a project and requires drying and attaining final strength. Moist concrete needs time to set and harden, which depends on various factors such as the concrete mix, weather conditions, and thickness of the concrete layer.
The use of moist ready-mix concrete has both advantages and limitations. Among its advantages are ease of transportation, better control of water-to-cement ratio during production, and the ability to adjust the concrete’s strength by modifying the water content. However, the need for time to dry and achieve final strength can pose a challenge.
To effectively use moist ready-mix concrete, specific methods and timings for drying and strengthening the concrete should be considered. It is also recommended to carefully follow the manufacturer’s instructions and guidelines when using moist ready-mix concrete to optimize its performance and quality.
Dry Ready-Mix Concrete, also known as unset concrete, is a type of concrete that is delivered and transported to the project site in a dry state, eliminating the need for subsequent drying. Dry ready-mix concrete is typically produced using rapid-hardening methods such as the use of chemical additives or dry-mixing technology.
The use of dry ready-mix concrete has its advantages and limitations. Its advantages include no need for drying time after pouring, the ability to carry out immediate construction operations, and reduced construction time. However, dry ready-mix concrete may have limitations in certain conditions, such as a shorter service life and the need for specialized equipment and additives for rapid hardening.
To utilize dry ready-mix concrete effectively, appropriate methods and processes for drying and hardening must be followed. Additionally, it is crucial to pay attention to the manufacturer’s instructions and guidelines to achieve optimal performance and quality from dry ready-mix concrete.
Semi-wet ready-mix concrete is a type of ready-mix concrete that is in a state between dry and moist during delivery and placement on the project site. This type of concrete has lost some of its moisture and is in a semi-moist state. Therefore, unlike wet concrete that requires time to set and harden, semi-wet ready-mix concrete achieves acceptable strength immediately after pouring and requires less time for final curing.
Semi-wet ready-mix concrete offers advantages such as increased construction speed and reduced project duration. Additionally, it allows for rapid progression to the next phase of the project if needed. However, the use of semi-wet ready-mix concrete requires precision and specific conditions for transportation and placement to prevent issues such as quality degradation and strength reduction over time.
The use of semi-wet ready-mix concrete can be a suitable solution for projects with urgent or time-constrained requirements. To successfully utilize semi-wet ready-mix concrete, it is recommended to carefully follow the manufacturer’s instructions and guidelines, and adhere to proper conditions and scheduling.
Composite ready-mixed concrete is a type of ready-mixed concrete that is composed of a combination of various materials. In this type of concrete, careful collection and precise combination of different materials such as cement, sand, gravel, aggregates, water, and additives are utilized to produce a homogeneous mixture with desired properties.
By using composite ready-mixed concrete, it is possible to accurately and consistently control desired characteristics such as strength, durability, density, permeability, and compactness. This capability enables builders to select an appropriate combination of materials based on the specific requirements of the project, allowing them to achieve the best performance and quality.
Composite ready-mixed concrete is employed as a flexible and widely-used solution in the construction industry. Some of its advantages include ease of transportation, material and ratio precision, reduced construction time, and enhanced quality and durability. Utilizing composite ready-mixed concrete allows builders to achieve better coordination in construction projects and improve cost and time efficiency.
However, the use of composite ready-mixed concrete requires careful selection and combination of materials, along with the necessary knowledge. Additionally, to optimize the benefits of composite ready-mixed concrete, it is recommended to collaborate with reputable manufacturers and diligently follow their guidelines and instructions.
Steel beams, known for their high strength and stability, are vital elements in the construction of metal structures. By utilizing high-quality steel beam production while adhering to technical standards and regulations, significant improvements can be achieved in the performance and safety of structures.
Steel beams are extensively used in industrial buildings, bridges, warehouses, and other metal structures. They not only safely transfer electrical loads but also contribute to the overall strength and stability of the structure, acting as effective support systems.
In the process of steel beam production, quality and precision are of utmost importance. Selecting quality materials, employing advanced equipment, adhering to standards, and implementing rigorous quality control measures lead to the production of steel beams with desired properties and international standards.
The use of high-quality and standardized steel beams offers numerous advantages. They enhance the strength and stability of metal structures, increase safety, reduce costs and construction time, provide flexibility in design and installation, and accommodate diverse project requirements.
Overall, high-quality and standardized steel beams are considered vital elements in the construction of metal structures. By using precise and high-quality steel beams, it is possible to create reliable, stable, and optimally performing metal structures.
Concrete slabs, in addition to their use in architectural structures, have applications in various other industries. For example, in the oil and gas industry, concrete slabs are used as protective coatings for underground surfaces and pipelines to guard against corrosion and contamination. In the transportation industry, concrete slabs are employed as surface coverings for railway tracks and bridges to prevent wear and corrosion over time.
Furthermore, concrete slabs are utilized in civil engineering structures. In bridges, they serve as surface coatings on bridge decks and floors, protecting against corrosion, moisture damage, and environmental effects. Additionally, in reservoirs and water facilities, concrete slabs are used as internal linings for tanks and pipes to prevent water infiltration and corrosion.
Given the strength and resilience of concrete slabs, they can be effectively employed in harsh and challenging environments, effectively safeguarding structures against environmental damage and external factors. Therefore, the use of concrete slabs is widespread in various industries and in structures that require suitable strength and surface protection.
In general, concrete slabs are versatile concrete structures used in the construction industry and various other industries. With their positive attributes such as strength, durability, stability, and flexibility, these structures provide an effective solution for preserving and enhancing the performance and resistance of structures against external and environmental factors.
Advantages of Concrete Table Edges
1. Water Protection: Concrete table edges serve as a protective coating, preventing water and moisture from penetrating into the edges of the table. This feature increases the lifespan of the table and prevents damage and deterioration.
2. Corrosion Resistance: Concrete naturally has high resistance to corrosion. By using concrete table edges, the table edges are exposed to water and moisture, preventing corrosion caused by them.
3. Beauty and Style: Concrete table edges enhance the appearance of the table, giving it a beautiful and stylish look. The design and variety in color options for these concrete edges allow for choosing a desired look that complements the interior decoration style.
4. Easy Maintenance and Cleaning: Concrete edges have a smooth and non-porous surface, making maintenance and cleaning easy. The concrete surface can be washed and cleaned using common chemical agents, preventing the infiltration of dirt and stains.
5. Wear Resistance: Due to the strength and durability of concrete, concrete table edges have high resistance against wear and tear. This feature increases the lifespan of the table and reduces the need for repairs and maintenance.
Considering the advantages offered by water-embedded concrete table edges, their use is prevalent in various industries such as restaurants, hotels, cafes, and residential homes. These edges not only provide practical and protective features but also contribute to the decoration and beautification of interior spaces.